In the modern era of engineering and construction, steel continues to dominate as one of the most versatile materials. However, with the demand for lighter and stronger applications, steel manufacturers are driven to innovate rapidly. Emerging lightweight and stronger steel alloys have shifted the landscape, placing a heavier reliance on adaptive casting mould technologies to cater to these evolving needs.
The New Age of Steel: Revolutionizing Material Science
The rise in demand for high-performance alloys stems not only from traditional industries such as automotive and construction but also from cutting-edge sectors like aerospace and renewable energy. Here are a few key reasons why lighter yet stronger steel alloys have become the focus of modern metallurgy:
Performance Requirements: Industries demand materials that provide high strength-to-weight ratios to enhance performance and efficiency. Whether it’s building skyscrapers or constructing jet engines, lightweight materials that don't compromise on strength are crucial.
Energy Efficiency: The shift toward greener operations means that reducing the weight of materials can lead to more energy-efficient operations be it lighter cars that consume less fuel or efficient machinery requiring less energy input.
Cost Consideration: Harder, more durable materials can reduce lifetime costs by decreasing maintenance needs and improving product life.
Adaptive Casting Mould Technologies
With the development of new steel alloys comes the necessity for more sophisticated and flexible manufacturing processes. This is where adaptive casting mould technologies have become invaluable:
Design Flexibility: With advanced computer-aided design and machine learning tools, manufacturers can now create dynamic casting moulds better tailored to specific alloy compositions and geometries. This versatility minimizes material wastage and optimizes the overall casting process.
Consistent Quality: Adaptive casting technologies ensure uniform cooling and solidification of the molten steel, which is crucial for maintaining material consistency and reducing defects like cracks or warpage.
Speed and Efficiency: These technologies significantly reduce the design-to-manufacture timeline, making it easier to produce small batches of specialized alloys while maintaining efficiency in large-scale productions.
Technological Integration in the Casting Process
The integration of advanced technologies within the casting process marks a significant development in producing steel materials. Some of these include:
Smart Sensors: By incorporating IoT-driven sensors, insights into temperature fluctuations and solidification rates can be gleaned, allowing for real-time adjustments and improving the quality.
Robotics and Automation: Automation streamlines operations, reduces human error, and enhances safety, especially during high-temperature casting processes, offering more precision and scalability.
Artificial Intelligence (AI): AI systems analyze vast datasets from the casting process to predict potential issues, optimize mould designs and improve decision-making during production.
Sustainability from the Shop Floor to the Finished Product
Adopting lightweight steel alloys combined with innovative casting technologies does more than enhance functionality; it also contributes to sustainability efforts:
Reduced Material Use: Innovative casting mould techniques lead to less material waste, conserving resources and reducing environmental footprints.
Eco-Friendly Production: The rise of electric arc furnaces powered by renewable energy sources highlights the industry's shift towards cleaner and greener manufacturing practices.
Challenges and Future Prospects
Despite these innovations, the industry faces some hurdles:
Adaptation Curve: As new technologies emerge, the learning curve for implementing adaptive mould technologies can be steep, requiring skilled technicians and engineers.
Initial Investment: The cost of integrating advanced mould technologies can be high. However, the investment often repays itself through operational efficiencies and reduced waste.
Material Limitations: While advances continue, there are still bounds to what lightweight steel alloys can achieve compared to traditional materials. Thus, ongoing research is essential to push these boundaries further.
Conclusion
The development of lightweight and stronger steel alloys represents an exciting frontier that has encouraged significant advancements in adaptive casting mould technologies. As innovation continues, the alignment of material science with intelligent manufacturing processes will pave the way for a future where steel remains not only relevant but indispensable. As businesses adapt to these changes, they hold the potential to lead the charge in sustainable, efficient, and future-proof production practices. By investing in and integrating adaptive casting mould technologies, industries are better equipped to meet the demands of tomorrow's challenges head-on.
Explore Comprehensive Market Analysis of Continuous Casting Mould Market
SOURCE-- @360iResearch
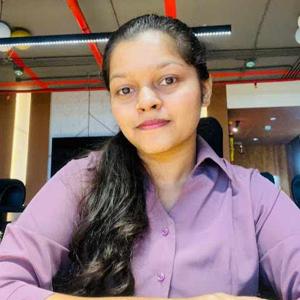
Write a comment ...